I occasionally fly with some old timers that still solder their line terminations. I said that wasn't a good idea, because of the stress raiser that is formed between line and termination. OK was the response what do others do? I glibly said that a lot of folk use epoxy instead of solder. The response was, well you still get a stress raiser at the epoxy / line joint. At that point, I shut up, not being able to find a suitable response!
The folk concerned have been flying for many decades with no accidents due to line parting. They are just very careful and inspect the lines each flight, when they take a rag and wipe the lines down before picking up the handle.
The moral of this is "inspect your lines frequently, whatever type of termination you use"!
Indeed, I wouldn't recommend trying to solder stainless steel. You won't be able to clean all the flux 100% and the remaining traces it will eat their way through your cables.
But I want to point out that the only eyelet I ever broke was on a set of Sullivan lines that were given to me, they were made exactly this way (with epoxy):
http://www.clcentral.com/images/Wrapping%20Lines.pdf Broken just where the wrapping ended....
Since I'm flying with lines that have a tin coating (3 strand Laystrate, now Staystrate), soldering is quick and easy. Always use rosin core solder, NEVER liquid flux! And use a small iron ( 30 watts or so)
And of course: DON'T solder the line, just the eyelet. The flexibility gradually increases going away from the eyelet. The flexing (if at all) always occurs over a distance of 40mm. Just soldering indeed is very wrong and may have catastrophic results.
How it's made:
Start off with a single knot (~ 8mm dia), and spin the loose end round the circle two times.
Then lead the loose end back around the line (~40mm) and same, back to the eyelet.
Go round the eyelet once more, and back along the line for 20mm and back.
Go round the eyelet one last time and cut the remaining loose end at 15 mm. Pry this into the 20 mm piece, spun round the line.
Pinch the eyelet to an oval shape.
Take fine copper wire and wrap the bottom 1/3 of the eyelet and part of the 20 mm braided piece along the line.
Just solder where the copper wire meets the eyelet. Solder will wick to the cable forming the eyelet, fixating it.
And that's all.
I'm using this method since 1969 and I haven't had a malfunction yet.
Inspect your eyelets et all, EVERY time you go out and fly.
These cables are the European alternative to solids I think, for when I pick up stainless multistrands they have that 'rubber band' feeling I don't like.
And they have a tendency to swing like a skipping rope and try to rock the plane ( OK, extra tip weight cures this for the greater part), something that is not as pronounced with the 3 strand lines. I'm flying .015, .018 stainless makes the described effects even stronger.
Here's what they look like:
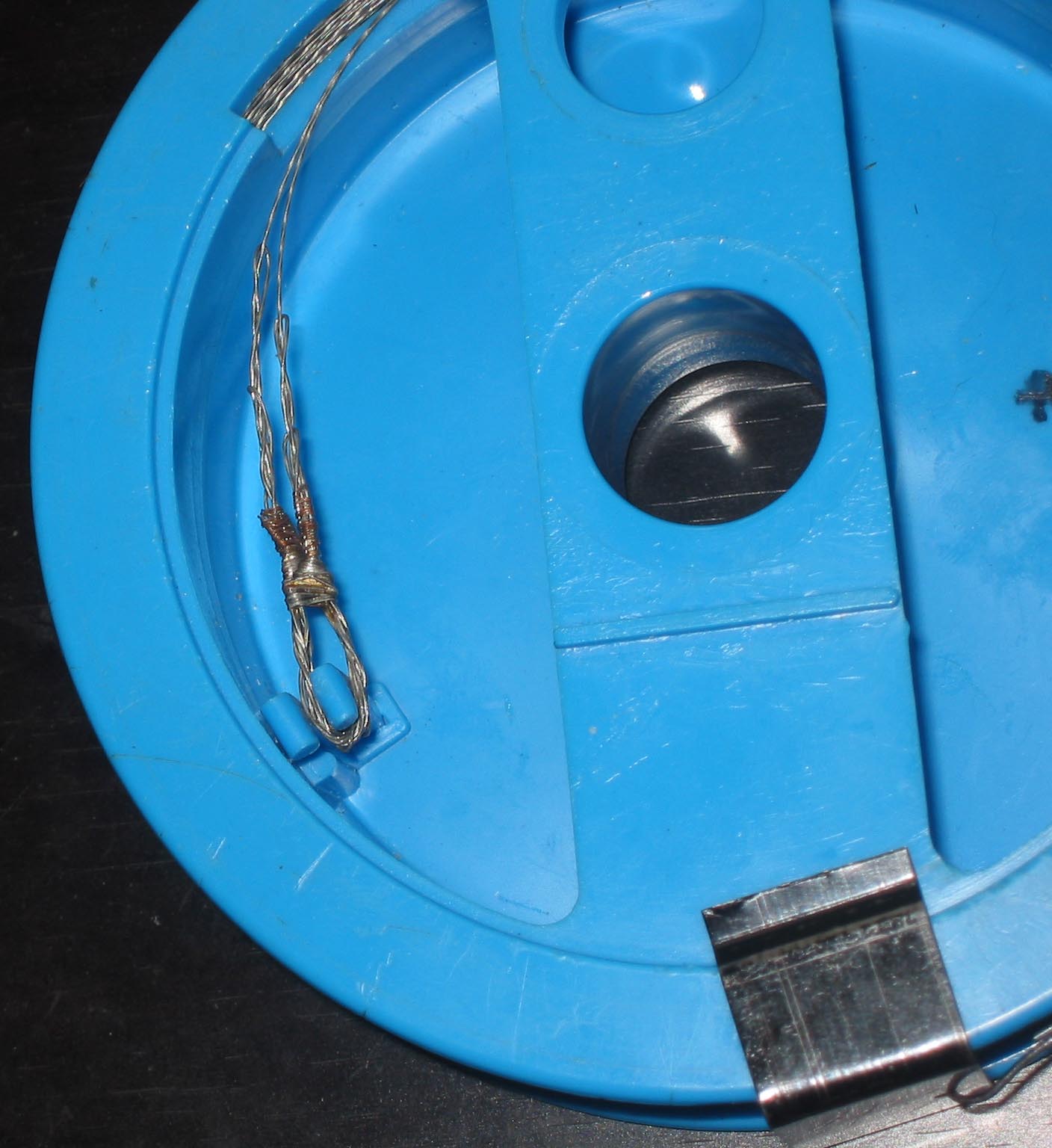
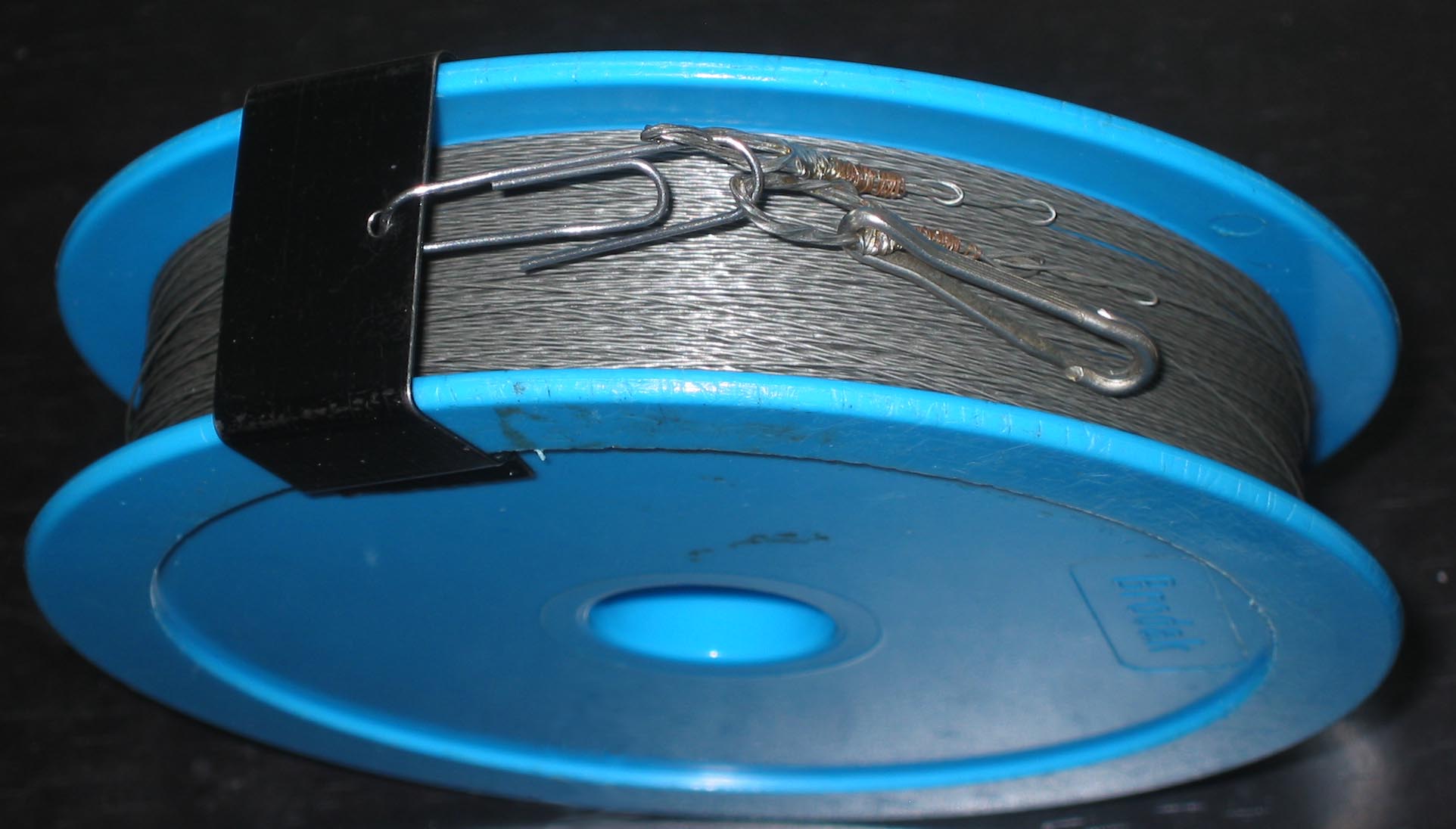